Electro-hydraulics are enhancing off-highway car performance and effectivity, enabling machine management and offering the constructing blocks for energy-recovery techniques. Trade specialists give perception into the evolution of this expertise and predict future developments
Over the previous three a long time off-highway car designers have moved away from constructing machines which have hydraulics managed by way of mechanical techniques and hydraulic pilot strains to utilising digital management – electro-hydraulics. However, whereas such techniques are nicely established, the complete prospects of this structure are nonetheless being explored.
Although hydraulic actions are nonetheless very a lot analogue in nature, the controls that operators use are nearly wholly now within the digital age, although the change didn’t come about in a single day, somewhat by way of a gradual evolution.
That is borne out by element specs. Danfoss, for instance, after years of designing elements that might be used with both mechanical or digital interfaces, has now fully transitioned its new elements to electro-hydraulics.
“The interface of our hydraulic merchandise has gone by three phases of evolution,” says Jeff Herrin, senior vp of R&D at Danfoss Energy Options. “The primary stage, courting again a few years, concerned hydraulic and mechanical interfaces. For instance, a hydraulic pump managed by a lever that an operator may use to create the specified circulate.
“The second stage launched designs with each lever entry and digital management. This transitional section was vital as a result of trade shifts don’t occur in a single day. We wanted a 10-year plan the place clients who wished the legacy answer may nonetheless get it, whereas we additionally constructed within the trendy, future answer of a digital actuator that they may management.
“As soon as we reached a sure degree of adoption, we moved to the ultimate stage: merchandise particularly designed for digital management. These don’t carry the luggage of mechanical gadgets, which add value and compromise designs.
“For many of our merchandise we’re already at this final stage so we not design future merchandise with legacy interfaces. If clients nonetheless want a mechanical interface, they will purchase the older technology, which we nonetheless produce. They’ve completely different efficiency and security ranges, however they continue to be obtainable.
“Our focus now’s on designing hydraulics with digital interfaces as a result of we all know the long run lies in electro-hydraulic techniques. Actually, 100% of our new product growth applications are focused in that route.”
New methods to maneuver
Not too long ago Volvo Development Tools has used electro-hydraulic structure in its new Impartial Metering Valve Expertise (IMVT), obtainable on 50-tonne EC550 and EC530 excavators.
“IMVT marks a departure from the normal mechanically coupled hydraulic techniques and introduces clever digital management with quite a few variables,” says Sejong Ko, Volvo CE’s product supervisor for big excavators. “The outcomes are as much as 25% improved gas effectivity and higher operator management.”
IMVT permits additional options utilizing a closed-centre valve-control system, which not like conventional open-centre techniques, can cease or reduce hydraulic circulate by the primary management valve when there’s no demand for a hydraulic actuator. This considerably reduces gas consumption and eliminates the necessity for an eco mode.
It additionally makes use of impartial cylinder management, sensing and controlling all sides of a cylinder’s chamber independently, with out utilizing hydraulic spools and pilot strains. This ends in extra exact management of the excavator’s actions.
“IMVT replaces conventional spools with poppet and electro-hydraulic valves in the primary management valve (MCV), decreasing stress losses and optimizing valve management primarily based on load situations,” says Sejong Ko. “This results in quicker cycle instances, improved regeneration and lowered circulate loss, with evaluation displaying a 20% increase in productiveness.”
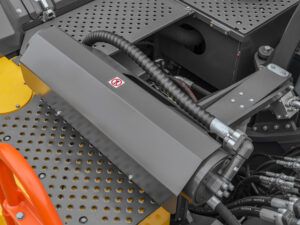
Hydraulic hybridisation
Regardless of potential vitality restoration ranges in off-highway car hydraulics being comparatively small when in comparison with the well-established hybrid techniques utilized in hydraulic braking for automotive; lately, tighter emissions targets and rising vitality prices have offered higher demand, significantly in excavators, which generate essentially the most carbon emissions of any car class within the off-highway world.
“But it surely’s not a trivial factor to do in hydraulics,” says Herrin. “It’s a must to add extra complexity with extra elements and circuits, and to do it, you completely should have an digital system.”
The worth proposition for that extra complexity has traditionally been pretty poor, with OEMs having to make the commerce off on complexity versus profit. However the rising push for sustainability is driving innovation. “We did a refresh on our industrial pump product line,” says Herrin. “It was designed 30 years in the past and is now being refreshed and up to date to trendy specs. The spec for this new pump was, actually, to have the ability to recuperate vitality in addition to pump vitality.”
In 2020 Volvo CE first introduced that it had developed a Hybrid system for its excavators which recovers vitality straight from hydraulic techniques, not primarily through the use of pumps, however as a substitute via a hydraulic accumulator. It captures and reuses hydraulic energy, leading to as much as 17% enhance in gas effectivity and 15% discount in CO2 emissions. Not too long ago the OEM introduced this Hybrid expertise can be added to its giant EC400 and EC500 40 and 50 tonne machines, having already been obtainable on 4 smaller automobiles within the vary – the EC380E Hybrid, EC350E Hybrid, EC300E Hybrid and EC250E Hybrid excavators.
“We do it by mounting a hydraulic accumulator simply behind the growth, and because the growth goes down, the high- stress oil that you just use to retard the growth dropping goes into the accumulator as a substitute of being routed to the tank,” says Dr Ray Gallant of Volvo CE. “This provides the accumulator a high-pressure cost that’s then routed by help motors and put again into the cylinders on the upswing. All the course of is managed mechanically – the operator isn’t required to do something. He merely sees a small image on the sprint that tells him when his accumulator is charging and discharging.”

Volvo CE’s hybrid hydraulic expertise doesn’t generate electrical energy or require batteries for storing it. “It requires minimal elements – there are not any electronics to program and no management techniques aside from system monitoring,” says Gallant. “Upkeep can be easy because the system is a primarily a mix of hydraulic circulate and valves.
There are different options which can be extra reliant on pumps being able to working in a bi-directional method. For instance, pump- managed actuators handle movement primarily by pace and/or displacement management of particular person pumps, making the pump a central element within the system. It’s on this area that promising applied sciences embody Danfoss’s Digital Displacement pumps, floating cup expertise, and high-speed pumps. “We anticipate these options to succeed in the market over time,” says Hongsuk Kim, head of excavator medium and hydraulic platform at Volvo CE. “Notably for electrically powered machines, the place bi-directional speed- managed pumps can recuperate vitality again to {the electrical} energy system.”
Sooner or later extra steps might be taken with hydraulic vitality restoration applied sciences. For instance, dead-weight compensation techniques. “These use extra cylinders and hydraulic accumulators working in parallel with the primary hydraulic movement management system and will provide benefits in particular functions,” says Hongsuk Kim. “These techniques are comparatively easy and shouldn’t face important hurdles to reaching market readiness.
“A extra superior answer is the frequent stress rail structure, which makes use of one or a number of semi- fixed stress ranges mixed with hydraulic accumulators. On this setup, pressure and pace are managed by hydraulic transformers and multi-chamber cylinders, which signify state-of-the-art expertise. Even these superior techniques require a number of independently managed valves, very similar to IMVT, demonstrating that our growth efforts in IMVT are paving the best way for future improvements in hydraulic vitality restoration.”
“Finally electrified linear actuation will remove hydraulic fluid on machines”
Electromechanical actuators
A lot of prototype automobiles, in addition to Bobcat’s manufacturing all-electric T7X and S7X compact monitor loaders and skid steers, have accomplished away with conventional hydraulics altogether and changed them with electromechanical linear actuators. Herrin sees continued evolution within the area. He notes that Danfoss Energy Options is investing in electromechanical actuators as
a complementary product line to their electrification portfolio. Whereas the use circumstances for this expertise are at the moment modest, Herrin anticipates that, “as electrification takes an even bigger maintain in off-highway gear, in the end electrified linear actuation will remove hydraulic fluid on machines. Rotary actuators (wheel drives, work capabilities) will likely be first, steering subsequent, and linear actuators final.
Volvo CE is already making use of electric-motor pushed actuators in a few of its excavators, and reviews constructive buyer suggestions. “You will need to observe that electrical motor-driven actuators can work along with hydraulics as an intermediate energy transmission medium or, in some circumstances, with out hydraulics altogether,” says Hongsuk Kim. “Nevertheless, each hydraulic and electrical techniques have their respective benefits and limitations. We don’t imagine that one expertise will absolutely dominate throughout all functions.
At Volvo, we aren’t dedicated to phasing out hydraulics however as a substitute deal with adopting the expertise that most closely fits our clients’ wants. We acknowledge the challenges related to electro-mechanical drives, particularly for linear movement functions. These challenges are much less pronounced for rotary drives, making them extra possible to exchange hydraulics now.”
Enabling automation
One of many key benefits of electro- hydraulics is that’s has enabled machine management – whether or not that be semi-autonomous driver help techniques or full automation, with the ability to management actions by way of digital techniques is a vital enabler.
“One among our flagship innovation programmes is round autonomy,” says Herrin. “There are only a few use circumstances for absolutely autonomous machines proper now, however there’s a complete lot for semi-autonomous, which imply operators will be much less expert, as a result of the machine can function itself in cycles which can be repeatable.”
This development in the direction of automation is driving the necessity for extra superior applied sciences. As Herrin factors out, “While you get into that house, AI and machine studying are required. It’s the core digital algorithm expertise that allows automation.”
This text first appeared within the October subject of iVT